 |  | | | |  |  |  |  | "At home" Composite How-To |  | |  |  |  |
Posted: Fri Oct 10, 2008 8:33 am |
|
|
dummyracer36 |
Senior Member |

 |
 |
Joined: 21 Sep 2008 |
Posts: 723 |
Location: St. Louis, Missouri |
|
|
 |
Quick carbon fiber “How-To.”
These techniques can be applied to any composite fabrics, be it carbon, fiberglass or Kevlar, or any combination thereof.
Be warned that unless you are very proficient at this process, the part you make the mold from has a STRONG possibility of being damaged or completely consumed!!!
All items required (except the carbon, but using plain weave fiberglass is much cheaper to experiment with) can be easily obtained at a local hardware store, auto parts store or a WalMart
Items required:
chop strand fiberglass mat
plain weave fiberglass (or carbon fiber twill weave)
polyester fiberglass resin and hardener
carnauba wax
mold release (experiment with different products if you dont want to order the proper stuff)
'Glad' brand trash bags (these are a poly-based plastic and will act as a “peel ply”. You will also want to poke many holes in this for the extra resin to flow through)
poly-fil (the stuff used to stuff pillows, this wicks away the extra resin and allows a “channel” for the air to flow through during the vacuuming)
FoodSaver brand vacuum machine
FoodSaver brand vacuum bags
sharp scissors
mixing cup
something to spread the resin (squeegee)
Popsicle sticks or tongue depressors
rubber or latex gloves
vapor certified mask
Getting Started: Preparation
Select a part/piece to be copied that is in the best possible shape; free of major cracks or dents. Most woods are not suitable for this, as the resin will bond to the part and not separate.
Sand the part to remove all blemishes, starting with #200 and ending with #1000 wet/dry. Remember, your finished part will only be as good as your starting part!!
Once it is sanded smooth on all surfaces to be reproduced, apply a minimum of 5 coats of carnauba based wax, (more coats if using car wax!) Meguire's offers a specialty wax for molds.
Allow the final coat to cure for at least 8 hours.
Spray or wipe down the part with a specialty mold release. I like the water based products, no fumes and very inexpensive. Allow to dry as per instructions.
Making the mold:
Place the part on a piece flat sheet metal or glass.
Cut pieces of fiberglass strand mat to fully cover the piece several layers thick, usually at least 4.
Mix the resin and hardener according to instructions.
Using a paint brush, paint the part very heavily with the resin.
Lay the first layer of mat on, using a Popsicle stuck to make sure it adheres to all contours. Pour more resin on the layer and spread around getting full saturation. Removing any bubbles as you go, repeat until you have at least 4 layers.
Allow to cure about ¾ of the recommended time.
CAREFULLY remove original piece from the still flexible mold.
Let mold cure for at least 24 hours
Using the mold to create the part/piece being copied:
Using sand paper, scuff the inside of the mold, removing any high spots. Fill any low spots or voids left by air pockets with autobody filler.
Sand some more, going progressively finer until your at #1000 grit wet. DO NOT skimp on this part!
Repeat waxing and mold release spray from above on the inside of the mold.
Cut several slightly oversized pieces of carbon, keeping in mind how the weave will lay and appear on the final product. Depending on the piece being made, I will use 2-8 layers.
Mix the resin according to directions.
Place one layer of carbon in the mold, pour a small amount of resin on the carbon.
Use a small soft plastic spreader (same type used for autobody filler) to evenly spread the resin.
Working quickly lay another layer of carbon on top and repeat the pour/spread until desired number of layers are achieved.
Place a piece of Glad brand trash bag on top of the entire piece, and a layer of “polyfil” (the stuff used to stuff pillows) on top of the trash bag.
Place entire mess into a “FoodSaver” bag. Then the bag into the vacuum machine. While it is pulling the air out, use your fingers to help force the carbon into the mold.
Let it cure for about ¾ the recommended time, then open the bag and very carefully remove the part from the mold. Set aside for 8-10 hours, and trim the extra carbon, wet sand the surface with #1000 sandpaper, then wax and polish or spray with clear coat.
And you're done!!! Enjoy your new carbon fiber part that no-one else has!!
____
Once you get the basic techniques down, the sky is the limit! But like anything else... it takes lots of practice to get really good results.
NOTE this technique will give a satisfactory result, but will not reproduce the finish of parts manufactured using the proper (and expensive) vacuum bagging machines.
NOTE: The FoodSaver food vacuum bagging machine was not intended for this type of use. I have no idea what damages may occur to this machine from this process!
i will add pictures of this process soon. |
|
_________________ "not tonight dear, i have a race in the morning" |
|
 |
 |
|
|
|  |  |  | | | |  |  |
 |  | | | |  |  |  |  | |  | |  |  |  |
Posted: Fri Oct 10, 2008 8:48 am |
|
|
yourdaddyjoe |
Supporting Member |

 |
 |
Joined: 26 May 2008 |
Posts: 4027 |
Location: Tatorville, USA |
|
|
 |
We are Dummies.... We need pictures...
Pretty PLEASE..... |
|
|
 |
 |
|
|
|  |  |  | | | |  |  |
 |  | | | |  |  |  |  | |  | |  |  |  |
Posted: Sun Oct 12, 2008 11:33 pm |
|
|
Slavia |
Moderator |
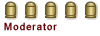
 |
 |
Joined: 31 Mar 2008 |
Posts: 4382 |
Location: Waseca, Minnesota, USA |
|
|
 |
Yes, pictures please! My wife got one of those vacuum things, and used it twice. It needs a new purpose in life. |
|
_________________
¡Listo! ¡Apunte! ¡Fuego! |
|
 |
 |
|
|
|  |  |  | | | |  |  |
 |  | | | |  |  |  |  | MOLD |  | |  |  |  |
Posted: Mon Oct 13, 2008 3:03 am |
|
|
kanyon |
Silver Status Member |

|
 |
Joined: 09 Aug 2008 |
Posts: 1582 |
Location: New Zealand |
|
|
 |
Fill & sand a completed mold????
If you had to do that I would have thought
the mold would have been trash.
Wax the plug "part to be copyed" with a mold release agent/wax 5 + coats
buff to a high gloss shine each coat then spray it with a laytex film let dry.
Then paint the part with Gell coat thinkly " The finish on the side you can see dose not matter its the surface against the part that counts"
when dry mold as meany GRP layers on as you like ..4.5 oz chop strand mat. Make sure you get complete wet out when layering up "no dry looking areas" use a brush in dapping motions brushing motions will move the strands around if the bit is big enough use a roller ribbed alloy ones are best. Between coats put the brush in the freezer to stop it going hard saves cleaning it each time.
GRP = Glass reinforced plastic "fiberglass"
When dry separate the part from the mold if the part is small enough
you can do it in water as the laytex layer will desolve in water.
If you do have to repaire small areas fill with gell coat & sand with the finest WET sand paper you can get finishing with rubbing compound.
use the same prep on the mold for the part to be layed up,,Wax / Laytex
mold wax & laytex should be obtained from a GRP outlet.
Use polyester resin for the mold its cheaper if the part is to be made in GRP epoxy resin is stronger but gell up time is very quick . If the weather is hot do it at night.
If your molds right so will the part you make.
As for the carbon..No idea not used it..But how hard can it be!
I made the nose cone on my last midget.
sizeing the image stuffed it a bit ...sorry
 |
|
|
 |
 |
|
|
|  |  |  | | | |  |  |
 |  | | | |  |  |  |  | |  | |  |  |  |
Posted: Mon Oct 13, 2008 5:27 am |
|
|
dummyracer36 |
Senior Member |

 |
 |
Joined: 21 Sep 2008 |
Posts: 723 |
Location: St. Louis, Missouri |
|
|
 |
kanyon, your right about using latex and gel coat, BUT the intent of this how-to was to alleviate the need to purchase alot of specialized materials for a first timer, also the process you describe is for "wet lay up", not vacuum bagging. with vacuum bagging you use ALOT LESS resin, therefor sanding out imperfections in the final part can be hard to do... theres simply not as much material that CAN be sanded away. i have been employing this basic method at the shop for years, making and selling fiberglass and carbon fiber body work for bikes. |
|
_________________ "not tonight dear, i have a race in the morning" |
|
 |
 |
|
|
|  |  |  | | | |  |  |
Note: If you are seeing "Please enter your username and password to log in." Your browser cookies have been reset
or you need to register to access the topic in question. Use the 'Register' button near the top left of this page.
|